Test and measurement system based on RXI test platform
RXI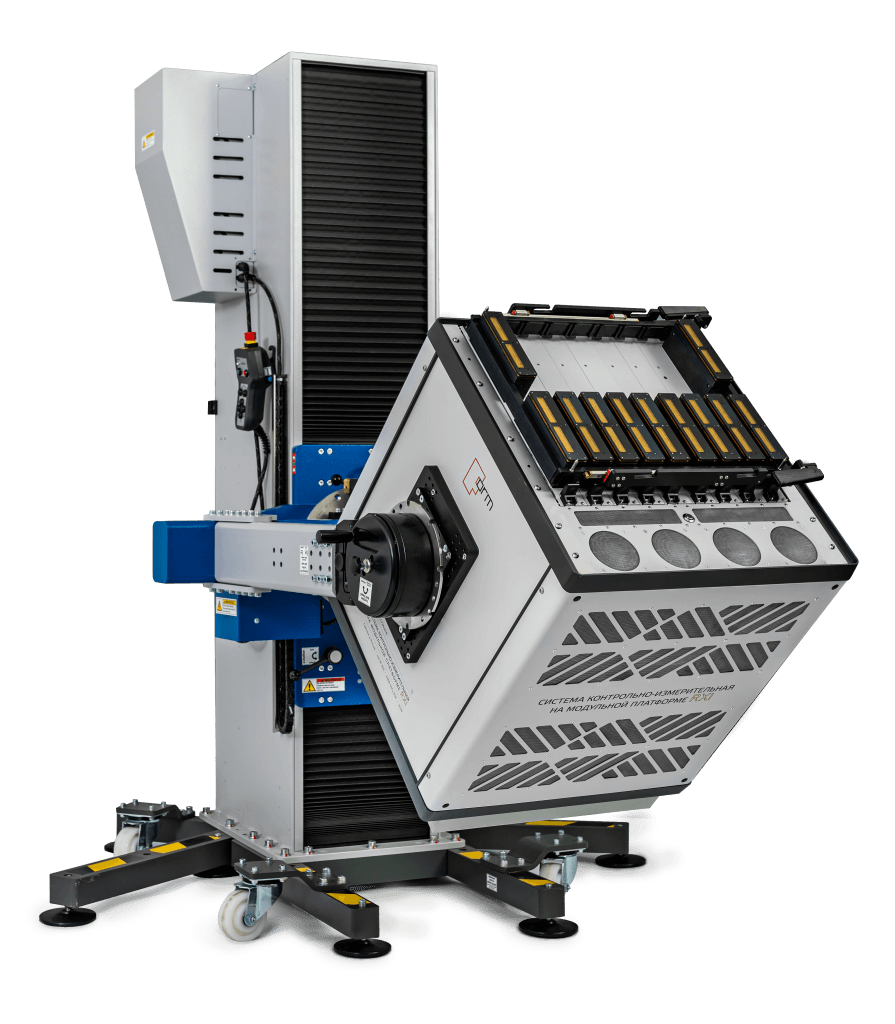
Developer and Manufacturer of RXI Systems:
FORM Ltd., Russia
The revolutionary modular architecture of RXI was created by FORM based on 29 years of experience in VLSI measurements and test equipment design.
RXI systems architecture makes it possible to expand system functionality by adding new instruments to the chassis, ensuring compatibility and synchronization across all instruments.
The new ATE-class allows addressing modern requirements and meets evolving test needs in the long term of up to 20 years — thanks to built-in development tools for improving functionality, characteristics and performance.
FORM company continuously uses the developed ATE in its laboratory for testing electronic components and, based on deep expertise, plans to develop a wide range of new instruments.
PURPOSE AND APPLICATION
The RXI system is the first modular ATE designed for metrological assurance of functional tests of all types of modern microcircuit:
microcontrollers, microprocessors, FPGA, SoC, SiP, ASIC containing DAC/ADC, memory units, serial interfaces, RF units; as well as static and dynamic memory circuits, when tested under high and low temperatures, as well as other external factors.
The application of RXI systems is testing and quality control at all stages of the IC life cycle, including
- Testing and research of newly developed types of microcircuits.
- Production and acceptance tests of serial products: qualification, periodic, screening, acceptance tests.
- Certification tests.
- Incoming inspection.
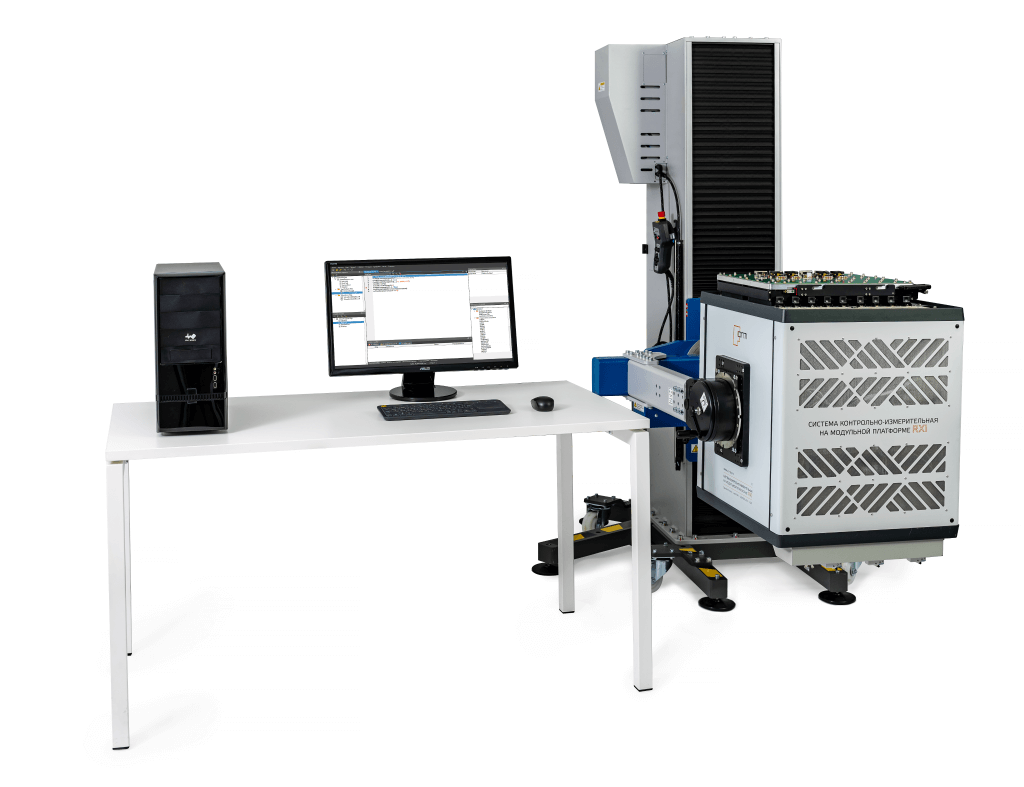
The RXI system
is the core for creating a metrological ecosystem of VLSI testing, highly adaptable to the growing spectrum and tasks in the field of VLSI quality control; integrating means of test and measurements, technological equipment, information system of design and production into a unified system of quality control of microelectronics in accordance with regulatory traceability procedures.
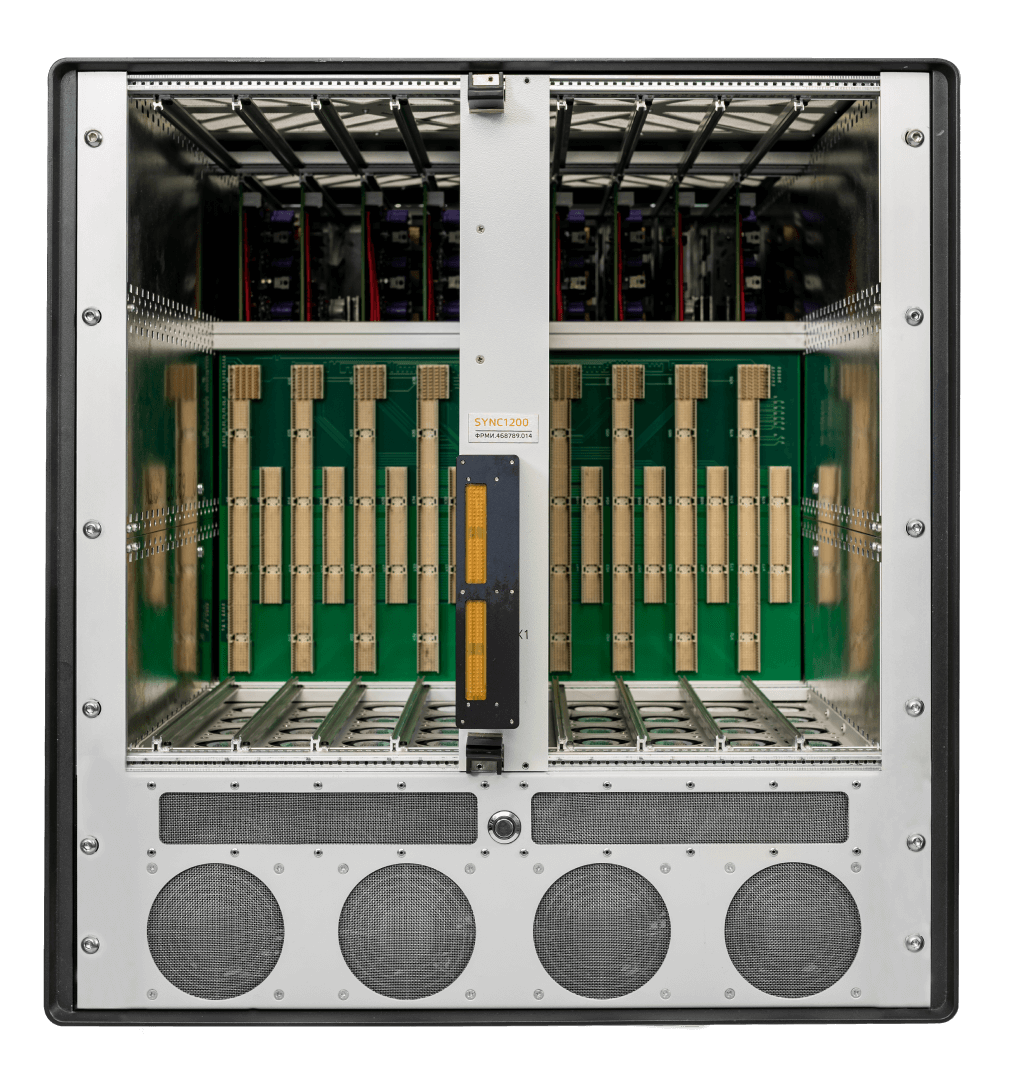
MEASURING MODULES BASED ON RXI STANDARD
The PIN400M measuring module provides a comprehensive automated functional test, measurement and control of the parameters of DUTs, comprising digital microcircuits of a large and very large scale of integration, including memory devices.
Each PIN400M module provides 64 universal bidirectional channels with a maximum data rate of 400 Mbit/s in the voltage range from 1.5 V to +7.0 V at the inputs and outputs of microcircuits, with the function of parametric testing of microcircuits.
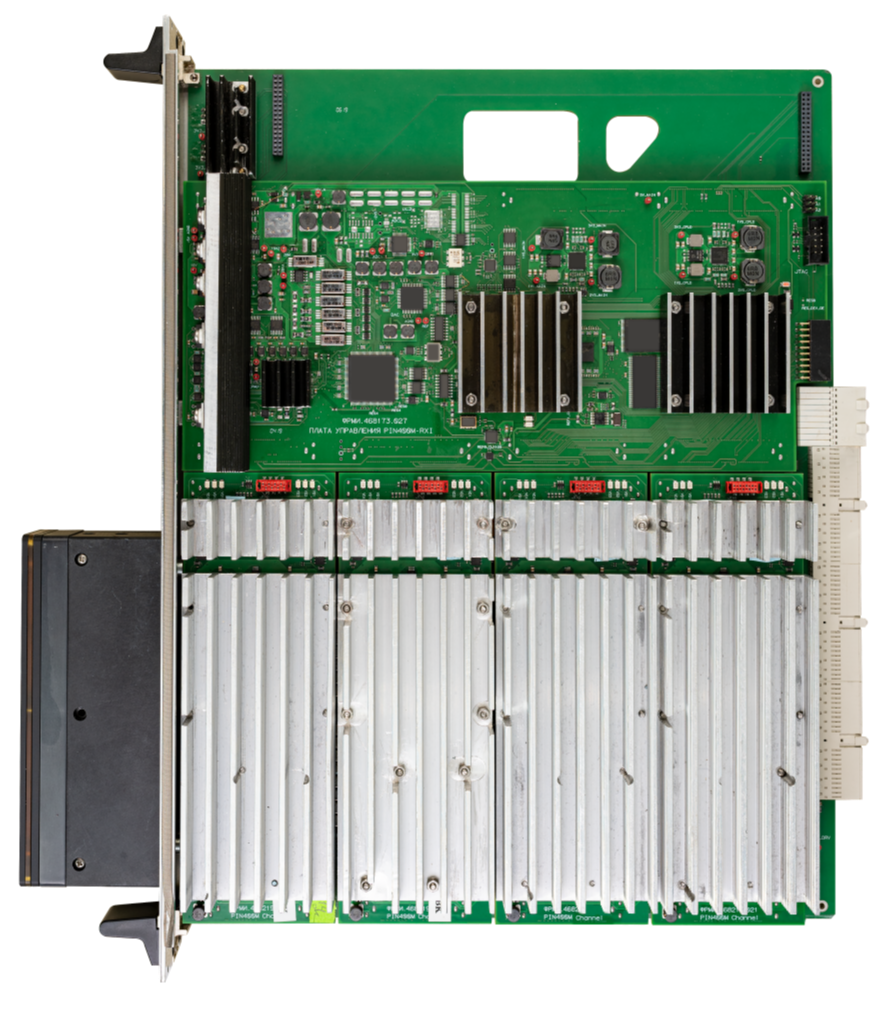
LNPS 10V modules provide a multifunctional low-noise 8-channe measuring power supply in the range of ±10 V, ±500 mA per channel, designed to power the devices under test, as well as to measure static parameters, including the conversion parameters of the ADC and DAC.
Each channel can generate signals in the form of a ladder diagram or constant voltage level.
The channels of the LNPS10V measuring module can be controlled by commands from other measuring modules, including from the vector sequence in PIN400M, as well as from external sources using internal and external trigger lines.
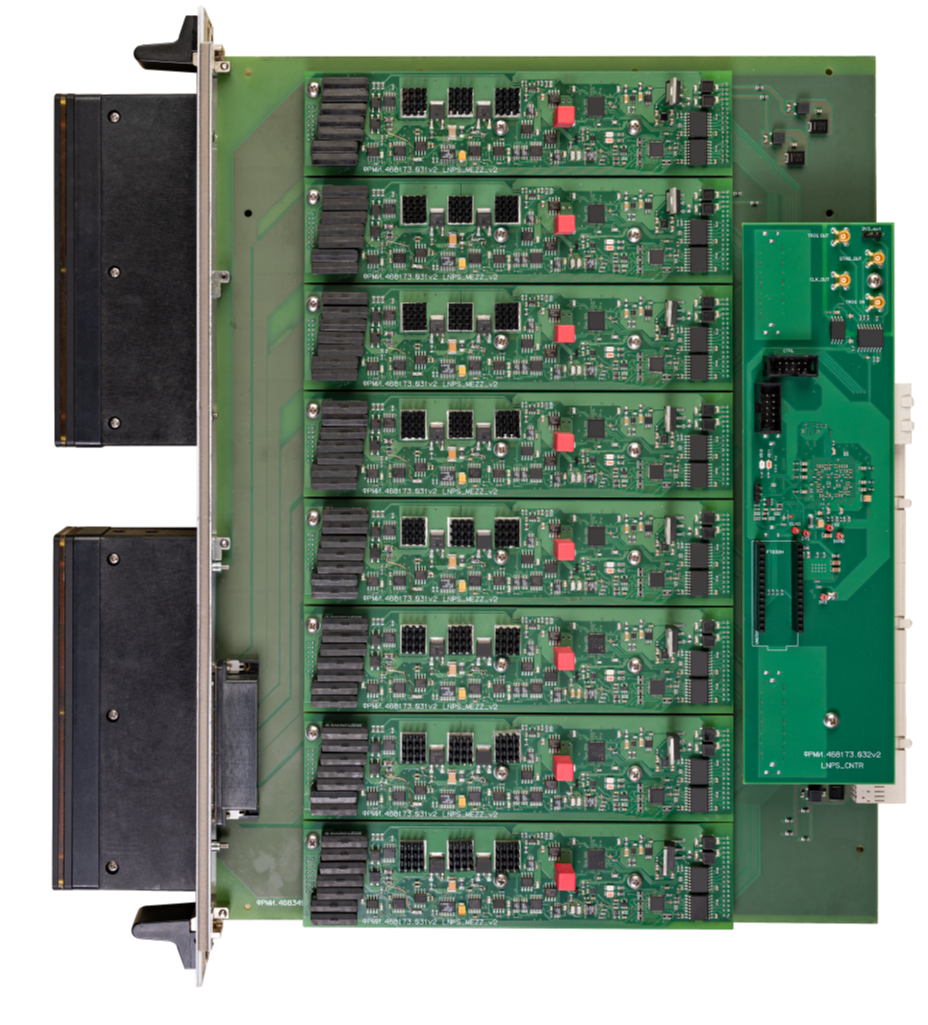
DPS (DUT Power Supply) module is designed for powering devices under test, including operation in multisite mode.
The module provides — 32, independent channels, generation and measurement of voltage in the range from -2.0 V to +7.0 V, current – in the range of ±500 mA per channel.
The module provides:
- Generation of voltage across the load
- Measurement of voltage across the load, including when channels are in the high-impedance state (leakage current is no more than 30 nA)
- Test and measurement of the current through the load when generating voltage across the load
- Limiting the current through the load
- Connection test of the 4-wire circuitry in the fixture
- Programming the settling time of the output voltage
- Parallel connection of channels on the fixture, to increase the load current (up to 32 channels connected in parallel).
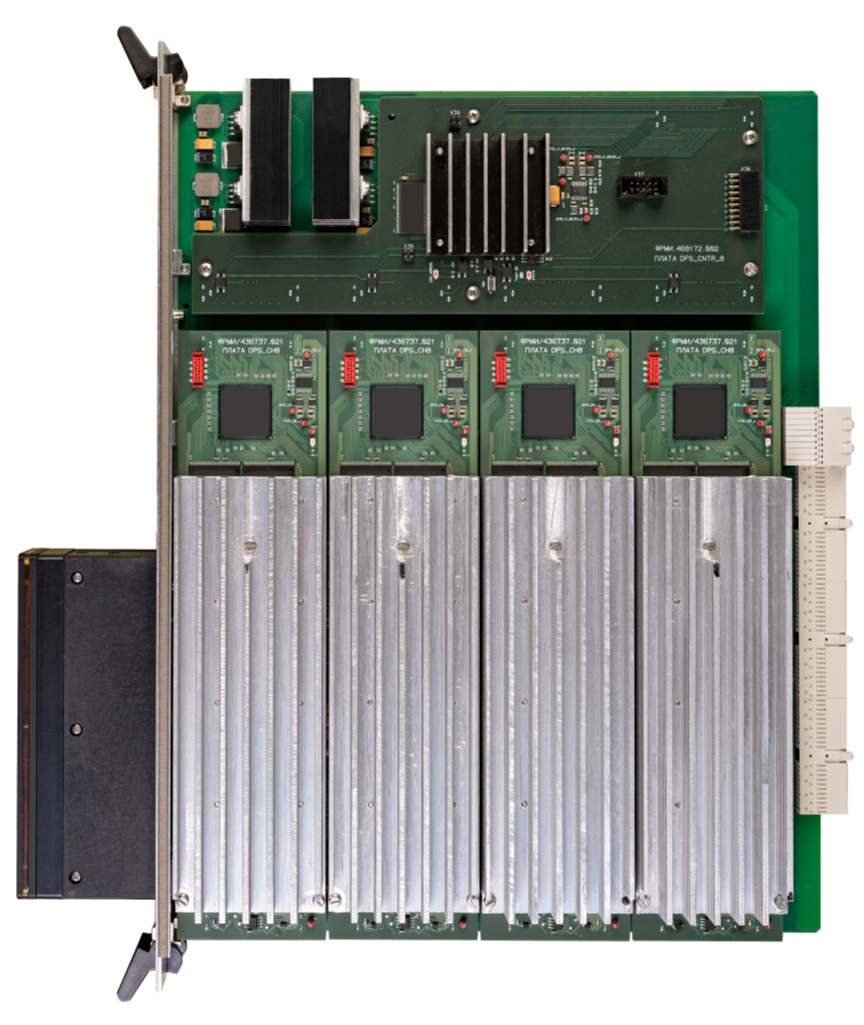
Each channel of the DPS measuring module can operate in one of the following modes:
- Force voltage, measure current
- Voltmeter
- High impedance state.
RXI SYSTEM SOFTWARE
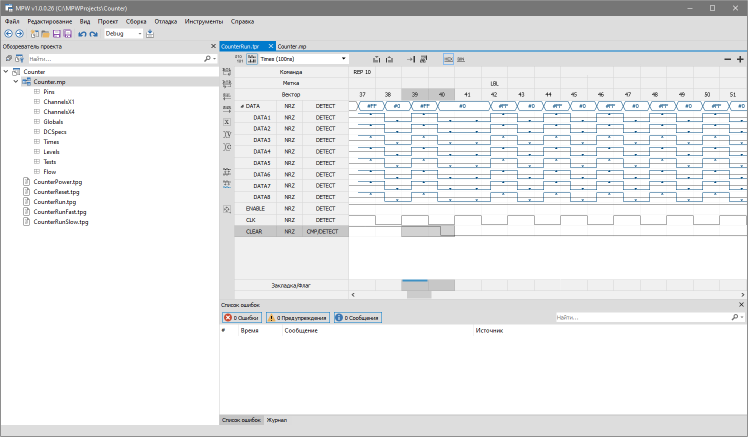
Test Pattern Editor
The RXI systems' software is designed using the most advanced programming technology while maintaining the familiar and well-proven interfaces of the FormHF Software for the previous generations of FORMULA Test Systems that have received high ratings in the industry, and continuously improved for 29 years. Recognition of the software allows engineers to reduce the effort required to develop and debug new test programs.
A single graphical user interface supports all phases and modes of application of RXI systems in customer configurations – from the development of test programs by engineering personnel to testing in production by operators.
The software service complex covers all aspects of the RXI system operation, including equipment performance monitoring, fault localization and metrological compliance verification.
Automatic generation of verification protocols is provided. As a result, the time for equipment maintenance can be minimized and at the same time give complete confidence in the correctness of the measurement results.
In operator mode, the software monitors and issues appropriate warnings about possible incorrect measurement results caused by a malfunction of the contacting device, contamination, lack of reliable contact, or other factors that occur at production facilities, which is important for automatic batch testing in mass production.
APPLICATION OF RXI SYSTEMS
IN THE PROCESS OF VLSI TESTING FOR EXTERNAL INFLUENCING FACTORS
The design and instruments of the RXI systems create the best conditions for testing microcircuits in the temperature range using the ThermoStream, as well as modern probe stations and handlers that create the necessary test environment for measurements.
Measurements under extreme temperatures are carried out directly on the board of the test fixture installed in the clamping device according to the hard docking principle, without the use of cables and loss of signal quality.
The manipulator allows the test head to be rotated in 3 degrees of freedom, providing the most ergonomic organization of the RXI system in the workplace.
TECHNICAL SUPPORT
DURING THE ENTIRE LIFE CYCLE OF THE EQUIPMENT
The location of a design office, production facilities, a service department and a certified metrological service on the territory of Russia, Moscow, allows urgent repairs of any complexity and metrological services throughout Russia, including by eliminating customs procedures.
Since the RXI systems are 100% developed by the Russian enterprise FORM Ltd, full support is provided for the life cycle of a new measuring instrument – from development to production and implementation.
During the entire period of operation, consumers are provided with consultations on work issues, assistance is provided in the development of test programs and equipment, additional training of consumers is carried out on demand.
The technical support service responds to any incidents during the operation of equipment in a strictly regulated time frame (no more than 1 working day).
COMPOSITION OF THE RXI SYSTEM AT DELIVERY
The RXI system is a turnkey test system, always ready to use, with a guaranteed implementation result.
The readiness for measurements on the day of delivery is an innovative advantage over other modular equipment based on open standards.
Metrological characteristics of RXI systems are provided at the system level – for any configuration, including the following components:
- Modular test platform;
- A set of measuring modules of various types;
- A package of high-level user software;
- Diagnostic and metrological kits;
- Manipulator;
- A set of operational documentation;
- Certificate of initial verification.
MANUFACTURER'S WARRANTY
Warranty service and support of RXI systems in operation are carried out by its developer and manufacturer – FORM.
The equipment warranty includes a free visit of FORM service engineers to the place of operation of the RXI system in case of warranty repair and extraordinary verification.