FORMULA® CK BOARD TEST SYSTEM
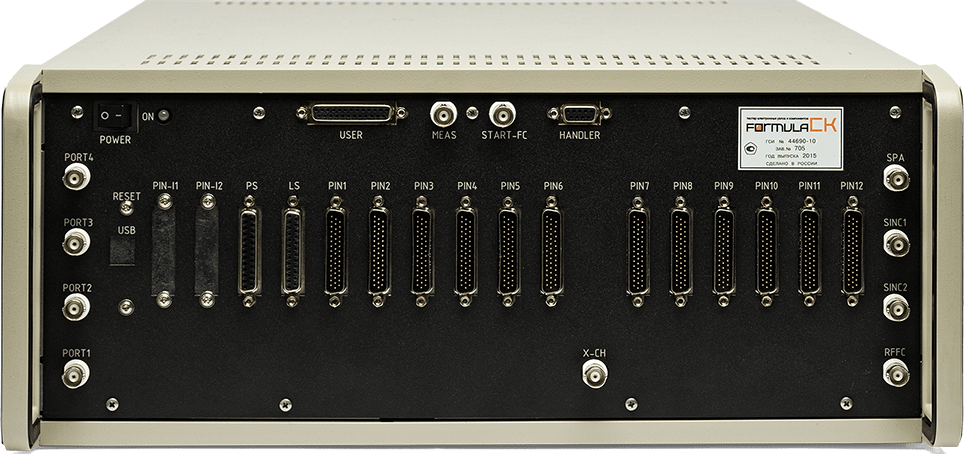
The FORMULA® CK Test System is an automated test and measurement system designed for functional and parametric testing of electronic equipment modules and assemblies, as well as their diagnostics and fault localization.
The application of the Test System is quality control, including acceptance, periodic and certification tests and measurements, other types of tests, as well as repair and testing of line-replaceable units in the stationary and mobile repair stations.
The FORMULA® CK complies with the Russian metrological standards for measurements and testing in microelectronics.
Developer and the manufacturer of the Test Systems:
FORM, Russia
BASIC TECHNICAL CHARACTERISTICS AND
FUNCTIONAL CAPABILITIES
The FORMULA® CK Test System is a functionally complete automated test equipment for performing acceptance tests of electronic equipment modules and assemblies and provides our clients with the following benefits:
- High readiness of equipment for measurements, tests, fault localization and maintenance functions
- Automation of all stages of the measurement process and data management
- Operating modes for working with external devices and equipment through a single Test Program
- User-friendly Software
- Automatic diagnostics and metrological calibration
- Reliability in round-the-clock operations
UNIVERSAL
MULTIFUNCTIONAL
SOLUTION
Implemented in the FORMULA® CK Test System Software compatability with external measuring instruments via LXI and GPIB interfaces, allows creating metrologically certified multifunctional workbenches that replace many highly specialized stands for testing modules of electronic equipment.
FORMULA® CK Test System is universal automated measurement equipment of the industrial type, fully ready for operation. Commissioning time of the integrated Test System-based Workbench is one day and allows to eliminate expenses on system-engineering design, software development, testing and certification of each specialized stand.
The Test System allows you to test the edge connectors and diagnose a wide range of electronic components: digital and analog cells, line replaceable units, subunits, blocks and other types of electronic components.
MAIN ADVANTAGES
Implementing the FORMULA® CK Test Systems in an enterprise allows to apply a unified approach to testing and diagnosing electronic assemblies, to implement standards on creating metrologically certified automated workbenches for conducting electronic modules acceptance tests and localizing failures. Means of integration with external devices and automated testing essentially form a built-in business process of electronic equipment assemblies quality control driven by regulatory, organizational, technical and metrological requirements.
This applies to test program development, the order of accessing approved programs and implementing changes, and automatic documentation of measured results and parameters, including metrological procedures and other regulated aspects of the process.
- Common User Interface (UI)
- Module for Integrating with External Devices
- Symbolic-Graphic Development Framework for Developing Test and Diagnostic Programs
- Debugging Tools
- Multifunctional Test Processor
- Automatic Data Collection / Processing Tools
- Means of Automatic Diagnostics and Metrological Procedures
MEANS OF INTEGRATION
WITH EXTERNAL EQUIPMENT
AND IT-SYSTEMS
The Test System is integrated with external measuring instruments for conducting tests of analog and digital-analog devices, power electronic units and other products. The means of integration comprise the 192×4 Integrated Hardware Switch and the Interface Module Software as part of the Test System Software.
The External Devices Interface Module is a set of universal procedures providing interaction of FORMULA® CK Test System with a wide range of standard measuring tools: voltmeters, oscilloscopes, frequency generators, etc.
The nomenclature of connected devices is not limited, at the same time all of them should satisfy only two key requirements — support the SCPI command language and the remote GPIB-USB-HS interface. Thus, it provides simultaneous connection up to 5 measuring instruments that can be operated by a single Test Program of the Test System Software.
Due to the simplicity of integration with external devices, based on the FORMULA® CK Test System, you can create Hardware and Software Systems to perform a wide variety of measurements, tests and diagnostics, which allows you to expand range and types of devices under test significantly, including analog and digital-analog assemblies and power supply devices. In addition, it is possible to organize a specialized and metrologically certified Workbench for each task at short notice.
Thus, using the Interface Module for connecting with external devices and the 192×4 switch allows to make the transition from particular solutions to general ones, significantly increasing the potential of the Test System and its benefits for the client.
To ensure compliance with traceability requirements, FORMULA® CK Software is connected to the specialized iLForm Quality Control Information System and provides a real-time transfer of measurement data to the enterprise server and other information systems of the enterprise in accordance with CALS standards.
Internal Switch allows connecting up to 4 external devices for testing analog and mixed signal devices. The Interface Module supports plug and play feature that significantly speeds up and simplifies connection of the FORMULA® CK Test System with external devices. It is user-friendly and does not require any special training.
FORMULA® CK
TEST SYSTEM SOFTWARE
The Test System Software significantly simplifies and speeds up the development and debugging of Test Programs, including the search of faulty components. It is adapted for use by wide-profile technical specialists. The library of high-level procedures includes standard methods for testing electronic equipment assemblies, as well as test compilation tools.
TestBox® TEST SOLUTIONS
The Delivery Set of the Test System includes complete instructions and documentation on how to connect external devices and develop a test fixture for connecting the electronic assemblies.
So that FORMULA® Test System clients can more quickly achieve their business objectives and promptly see a return on investment, FORM offers both factory-ready and custom TestBox® Test Solutions for measuring specific types of electronic assemblies.
TEST SOLUTIONSMANUFACTURER’S SERVICES
To reduce the client’s time and costs for support work, FORM offers the following technical services:
- Integration of FORMULA® CK Test Systems into the client’s technological, informational and testing infrastructure, with connection of external equipment, instruments and IT networks
- Scheduled maintenance, repair and metrological services at the place where the ATE is operated
- Organization of workstations based on FORMULA® CK Test Systems with a database for ensuring traceability of measurements
- Expansion of the ATE configuration according to a list of typical options, or with custom development of options